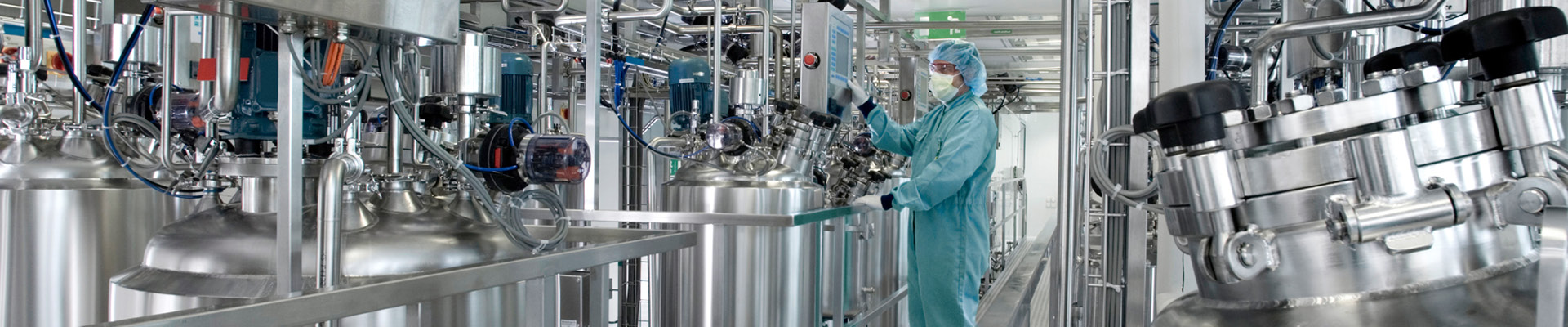
PROCESS ANALYTICS
Monitoring CIP/SIP Processes
Monitoring CIP/SIP Processes
In pharmaceutical, biological, and process plants for food production, all wetted plant components must be cleaned and sterilized at regular intervals. This is why all relevant tubing and tanks used in the Cleaning in Place (CIP) and Sterilization in Place (SIP) methods are rinsed and disinfected with the respective process-specific alkaline and acidic cleaning agents.
In SIP, the process plant is additionally sterilized with superheated steam for full disinfection.
The conductivity sensors for monitoring the cleaning process and the cleaning agent concentration in the rinse water must withstand frequent, extreme temperature changes and aggressive cleaning agents.
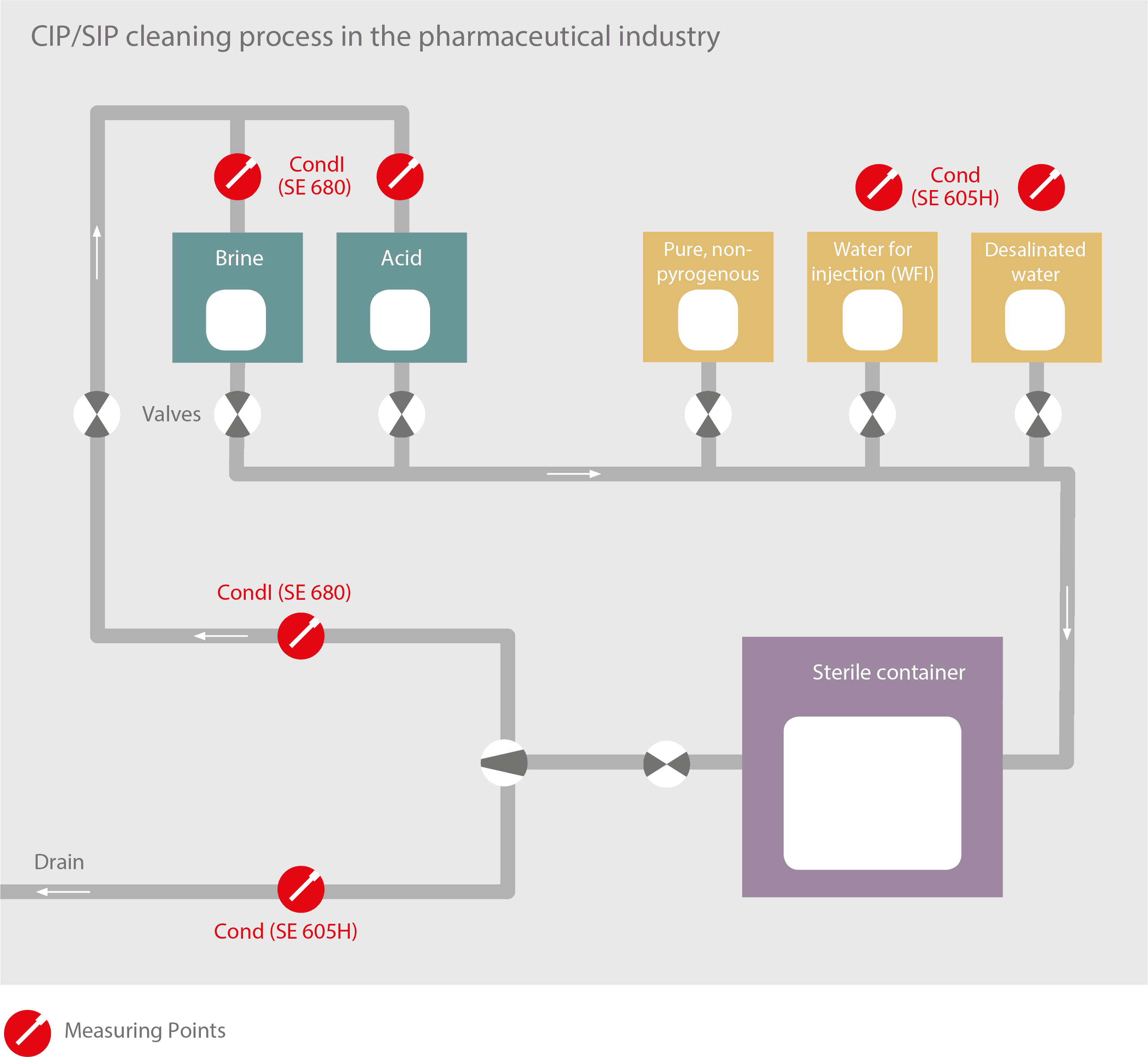
Reliable Conductivity Measurement for Extreme Temperature Differences
In CIP, coarse soiling is first removed by pre-rinsing with water and cleaning agents and in the rinsing operation, residual cleaning agents are eliminated. Next, acidic cleaning solutions are used to remove lime and other mineral deposits until in the last steps, disinfectants are introduced and the final rinse – flushing with ultra-pure water – is carried out.
In this cleaning process, the conductivity of the rinse water must be measured after every step to receive information on the remaining foreign matter in the water. If the measured values do not match the required specifications, the respective step is repeated until the setpoints are reached.
The SIP process follows immediately afterward. In SIP, the process plant is not only disinfected, but also sterilized by introducing hot ultra-pure steam (> 120 °C). Depending on the specific processes, batch sizes, and product variance, some plants must be cleaned and sterilized several times a day – in some cases, every hour.
The conductivity sensors used here are exposed to highly fluctuating temperatures (SIP ≥ 120 °C) in a moist environment. The conductivity sensors must have a robust and, above all, hygienic design. They are equipped with sector-specific process connections and are available in FDA-compliant materials.
The hygienic, inductive SE680 conductivity sensor for monitoring CIP rinse cycles features an extremely broad measuring range of 0 … 2000 mS/cm at a resolution of 2 μS/cm. The sensor seamlessly monitors the entire cleaning process.
Thanks to its seal-free, joint-, and gap-free design and contaminant-repellent surface made of FDA-approved virgin PEEK, SE680 is highly robust, particularly in the pharmaceutical sector.
For the final rinse with WFI (water for injection purposes), the ultra-pure water must have a non-temperature compensated conductivity value of < 2.7 μS/cm as a rule. Higher values indicate that residue is still in the water, which must be subjected to further rinsing.
The SE605 H contacting sensor, which was designed for the ultra-pure water measuring range of 0.001…600 μS/cm, is used to monitor the final rinse. SE605 H has a hygienic design with two coaxially arranged electrodes made of electropolished 1.4435 stainless steel with a surface roughness of < 0.4 μm or < 0.8 μm. All the materials used are FDA-compliant.
To transmit the measured values from the Memosens sensors to the control system, MemoRail industrial transmitters that transmit sensor and temperature values directly to the control system via the 4-20 mA output signal are available. For Modbus-based control systems, a MemoRail variant with the relevant interface is also available. As a multiparameter device in a compact, space-saving modular housing, MemoRail in the 1- or 2-channel variant can be universally used for all Memosens sensors for measuring pH/ORP, oxygen, and conductivity.
Return on Investment
- Memosens technology focuses on the economic efficiency of the measuring loop. Using Memosens reduces the investment costs for process analytics many times over. Two 2-channel Memosens sensors can be connected to the MemoRail multiparameter transmitter at the same time. The streamlined, compact modular housing simplifies installation in any system – even when space is at a premium – and transmits the measuring signals directly to the control system via 4-20 mA or Modbus.
- In addition, Memosens reduces and simplifies the maintenance effort for the measuring loop since the calibration data of Memosens sensors is saved directly in the sensor head. The robust, digital conductivity sensors monitor the process reliably and precisely.