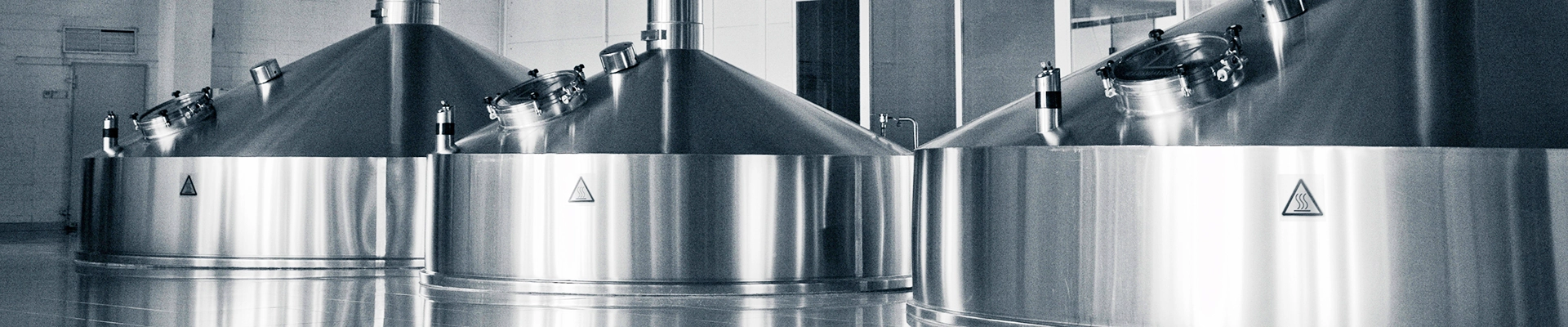
PROCESS ANALYTICS
Monitoring Brewing Processes
Monitoring Brewing Processes
The taste and quality of beer are highly dependent on the quality of the water used for brewing it. Its quality is determined by pH and conductivity measurements.
Globalization is putting lots of competitive pressure on breweries. Guaranteeing consistent beer quality is the key to surviving in the markets.
By using process analytics, quality can be ensured while optimizing process control at the same time.
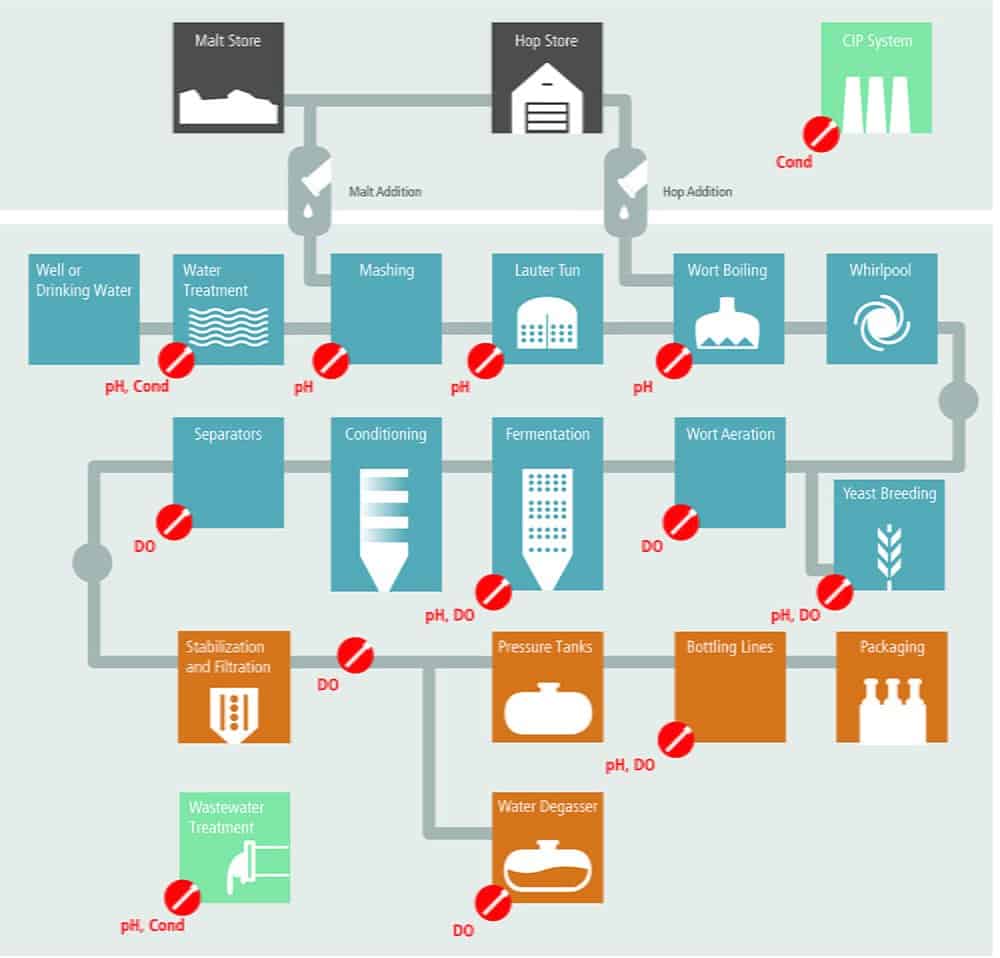
Starch-to-Sugar Conversion in the Mashing Process is Highly pH Dependent
In the downstream processes as well, pH measurement plays a key role. After the brewing water is mixed with milled brewing malt in the mash tun, enzymes turn the starches it contains into malt sugar. This process is strictly pH-dependent and takes place in the pH range between 5.4 and 5.6. In the next step, the resulting “wort” is boiled together with hops to control the flavor and shelf life of the future beer, determine the wort content, and lower the pH value. Since it is steam-sterilizable and biocompatible, the SE555 pH sensor is ideal for controlling these processes.
Oxygen Measurement – Indispensable for Safe Process Control
Next, the solid particles in the hopped wort – undissolved hop components (trub) and coagulated protein – are separated out in the whirlpool and yeast and oxygen are added to trigger alcoholic fermentation. Very strict regulations apply to the yeast. To ensure optimal quality, the pH value and dissolved oxygen levels are monitored during yeast breeding. Since the latter determines both yeast vitality and flavor development during fermentation, oxygen measurement is indispensable for safe process control. At this point, the SE706 oxygen sensor in the hygienic stainless steel design ensures reliable inline measurement.
As the wort is maturing into green beer in storage tanks, a low oxygen content ensures that it retains its flavor. Continuous oxygen measurement can also detect storage tank leaks in time. Before it is bottled, beer is filtered and stored in pressurized tanks. To safeguard the flavor and prevent oxidation, limit values for maximum oxygen concentration must be complied with. Some large-scale breweries configure the precise alcohol content of the beer by diluting it with degassed water. Measuring dissolved oxygen controls the degassing process. The same applies to bottling, in which the oxygen concentration usually has to remain below 25 ppb for reasons of shelf life and flavor.
CIP: Metering Rinsing Media with Inductive Conductivity Measurement
To comply with the stringent hygiene regulations in food production, the plants involved in beer brewing are cleaned in the CIP process. This involves the alternating flushing of a caustic soda solution and acid (often nitric acid) through the plants at temperatures of around 65 °C. The concentration of the CIP media (intrusion) is controlled based on inductive conductivity measurement with the SE680 sensor. In the final watering, the cleaned process lines are rinsed with water and the SE605 H contacting conductivity sensor is used to verify that all rinsing media have been completely removed.
Brewery Wastewater Treatment
Last but not least, Memosens technology such as the SE554 pH sensor, the SE655 sensor with high chemical resistance for measuring inductive conductivity in highly contaminated media, and the SE715 oxygen sensor with long-term stability are also used in the treatment of brewery wastewater. Since the treatment of brewery wastewater involves an unusually high load of trub, Knick recommends using automated cleaning systems at the affected measuring loops.
Return on Investment
- The contact-free inductive plug-in system of Memosens sensors ensures unrivaled reliability and measurement quality in the moist environment of breweries and for plant cleaning.
- Reliably precise measurements are the essential basis for high product quality and they permanently safeguard the brand properties that are decisive from the consumer point of view.
- Cost reduction thanks to increased sensor service life: Memosens detects the number of CIP/SIP cycles and provides recommendations for maintenance intervals in order to extend the service life of the sensors.