过程分析
制浆造纸过程控制
除了多种化学品外,制浆过程中还使用大量烧碱溶液和二氧化氯。
用于过程控制的 pH 传感器在与化学品持续接触时会承受很高的负荷。
此外,由于过程介质的纤维和悬浮物含量较高,短时间后就会在测量电极上形成严重的沉积和结垢,传感器的使用寿命因而受到限制。
腐蚀性化学品和高度污染使得过程环境甚为恶劣,需要能够在最短的时间内快速、轻松地更换传感器的测量回路。
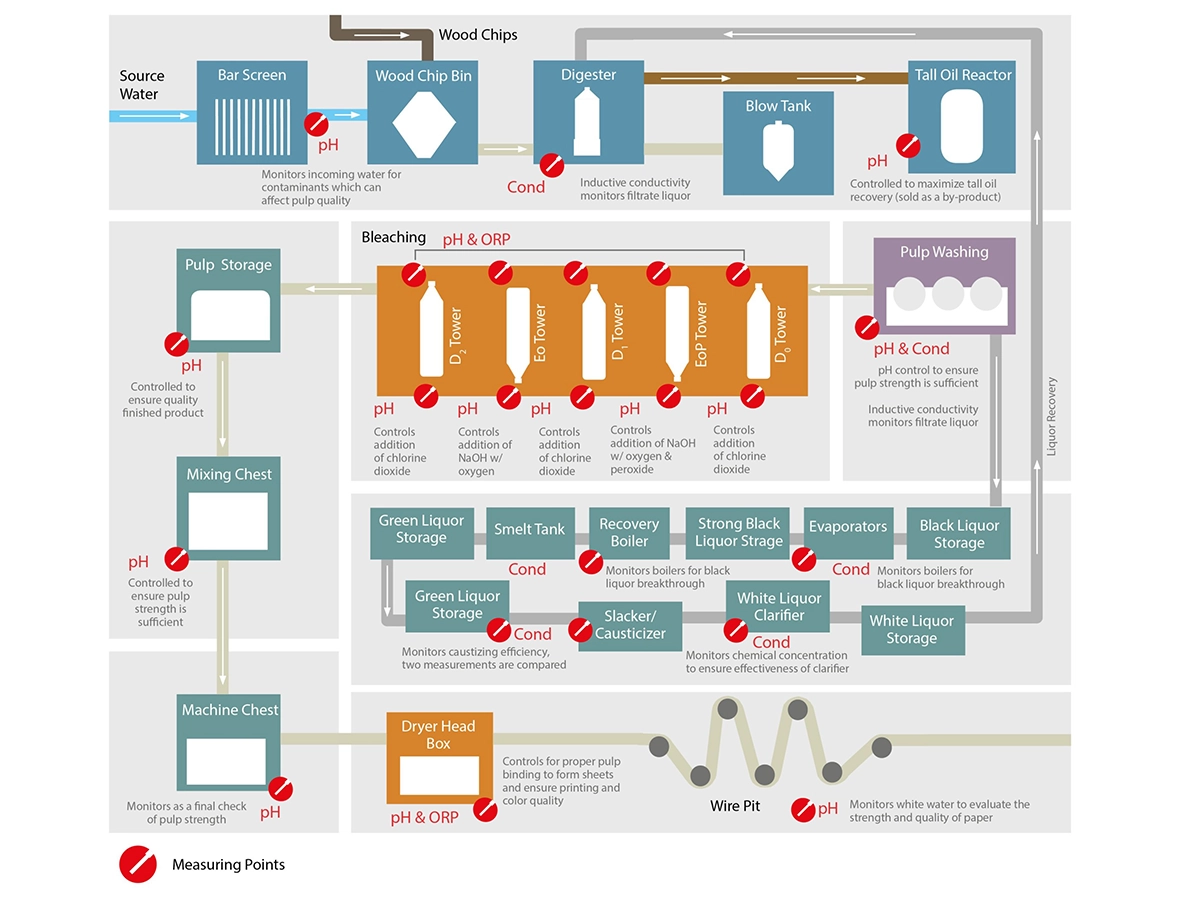
用于制浆造纸过程控制的测量传感器
纸浆生产过程
自从 19 世纪中叶发明了磨木浆纸以及所谓的硫酸盐和亚硫酸盐法以来,便能用木材造纸。在硫酸盐和亚硫酸盐法中,机械分离纤维的木材通过在烧碱溶液和含有硫化钠或二氧化硫的溶液中蒸煮进行化学分解,以去除所含纤维素纤维中不需要的成分。这些尤其包括形成木材的木质素、被称为“半纤维素”的多糖以及树脂和矿物质。在各种多级后续工艺对水溶液形式的纤维素纤维进行净化和漂白,分离出的树脂则用于生产妥尔油,妥尔油经过提炼后可用于生产肥皂和油漆。
制浆造纸的流程
除了基本的原材料特性之外,纸浆在加工过程中经历的各种净化和混合工艺的质量对产品质量起着重要作用。主要包括硫酸盐工艺中使用“白液”蒸煮纸浆,随后在过滤机中对蒸煮过的浆料进行过滤和洗涤,以及交替使用各种氧化剂处理纸浆的多级塔漂。
被称作“浆料”的纤维浆随后进入“浆料制备装置”。在那里首先将其按配方在混合槽中与各种纤维混合,进行研磨并加入高岭土、碳酸钙、胶水和染料之类的填料,以达到后期纸张的所需特性。在“流浆箱”中将纤维浆从喷嘴或孔板均匀喷涂到筛网上进行脱水和曝气,筛网将其送入造纸厂的压榨部和干燥部。
生产过程中的关键测量回路
在制浆的各个生产阶段,众多的 pH 和电导率传感器必须确保过程质量。特别是在蒸煮或塔漂过程中,木浆的过度化学分解或漂白剂用量或残留物控制不当都会损害纤维并降低其强度。只有在最终检查纸板或纸张撕裂长度、撕裂和破裂强度的环节中才能发现此类损害。因此必须检查、控制化学分解的强度。做法是利用电导率测量来监测纸浆蒸煮装置中的白液浓度。
由于高温过程介质碱性强而且污染严重,所使用的电感式电导率传感器 SE655 采用耐腐蚀的 PEEK 制成,其坚固耐用的设计已得到验证。该传感器专为在污染严重且形成沉积物的介质中测量酸或碱浓度而设计,其电极与介质不会直接接触。相反,SE655 具有一个大的环形传感器开口,可将污染风险降至最低。SE655 设计用于 0.002 至 2000 mS/cm 的宽测量范围、-20 至 110 °C 温度范围,能承受高达 20 bar 的压力。
塔漂过程中的 pH 测量和氧化还原测量
氧化还原和 pH 测量在塔漂过程中起到重要作用。漂白过程用于去除剩余的残留物,如残留的木质素。在塔形容器中多个阶段交替使用二氧化氯和氢氧化钠(或者在更先进更环保的工艺中使用过氧化氢、氧气和臭氧)处理纸浆。
漂白过程基于漂白剂和被漂物质之间的电子交换。漂白剂的效果取决于其氧化电位的大小,可通过氧化还原测量予以确定。含固体物质的介质会迅速导致传统传感器的参比系统堵塞,所以在这里使用 Memosens 氧化还原传感器 SE564,该传感器通过双重多孔隔膜排除了这种风险。其参比系统采用现代聚合物电解质,可确保长期稳定测量 –1500 mV 至 1500 mV 的电位。
每次漂白之后洗涤纸浆,在其与下一个塔中的其他化学品接触之前,必须先利用 pH 测量检查漂白剂残留情况。每次洗涤之后,使用低维护的 Memosens 传感器 SE571 检查 pH 值,该传感器专为在污染负荷高而且离子强度极高的介质中进行测量而开发。其参比系统通过 PTFE 隔膜环与过程介质接触,最大程度降低了污染或堵塞风险。该传感器还配有储盐罐可防止浸析。带银离子阱的特殊筒式参比元件可防止参比系统中毒。
回收所使用的化学品
回收所使用的化学品对纸浆厂的经济运营至关重要。因此,纸浆生产过程中的大部分设备都用于处理在过滤/洗涤蒸煮分解的木纤维时所产生的黑液。黑液最初的固体含量高达 20%。利用蒸发浓缩设备将其提高到大约 80%,现在产生的浓液可以加入硫酸钠进行焚烧。
将所释放的能量转化为电流和过程热量,纸浆厂就可以满足其总能源需求的很大一部分。同时,在焚烧浓液时会剩下由碳酸钠和硫化钠组成的熔体,将其溶解于水中就会变成所谓的绿液。随后将绿液与石灰乳进行苛化反应,产生氢氧化钠以及白泥,通过过滤或者沉淀将其分离。从绿液获取的白液可在蒸煮过程中再次使用,而分离出的石灰则可在干燥和烧制后再次用于产生白液。
SE630 型 Memosens 传感器用于测量电导率,除了各个纸浆洗涤段之外,在黑液循环系统的不同工位中也需要测量电导率。电导率传感器的测量范围为 10 µS/cm 至 20 mS/cm,可承受高达 16 bar 的压力和高达 135 °C 的温度。其耐化性、耐热性、耐机械性很高,而且易于清洁,使用方便灵活。例如在化学品回收循环中,也可用于黑液锅炉的浓度过高监测,以及检查绿液苛化反应的效率。
技术人员的安全
制浆过程中的许多测量回路都位于必须尽量减少技术人员在场的环境中。由于腐蚀性过程介质的固体物质含量高,尽管传感器采用了牢固耐用的设计,其使用寿命也有限,但是能减少维护工作量,从而显著减少人员在测量回路的停留时间:使用预校准的 Memosens 传感器,完全不必进行现场校准。此外,与硬接线电极不同,Memosens 传感器采用卡口连接的快插接头,可在极短时间内完成插拔。
Memosens 传感器接头以感应方式传输传感器数据和馈送电压,完全不受湿气和沉积物的影响,因此无需任何电缆管理,而这在更换传统产品时是必要的。为了使用 Memosens 传感器进行在线测量,除了适合各种应用情况的过程连接之外,也有 SensoGate 系列的伸缩式连接件可供使用,这些连接件可以每隔一段时间全自动移出传感器,对其进行清洁、校准并将其重新移入到过程中。
这些伸缩式连接件的冲洗室与过程完美密封,因此可以在全额过程压力下进行传感器维护。可以手动操作的伸缩式连接件 SensoGate WA131M 为迅速更换直插式传感器提供了一种特别经济的解决方案。