프로세스 분석
증기 발생기 모니터링
증기 발생기는 다양한 공정에서 중요한 역할을 합니다. 이 장치는 발전 공정에서 발전기 또는 터빈에 증기를 공급하며 증기 기관을 구동하고 열병합 발전소에서 에너지를 제공하거나 화학 및 금속 산업에서 열을 사용하는 공정에서 사용됩니다.
증기 발생기는 애플리케이션에 필수적인 기능을 수행하고 다운타임 또는 교체 시 막대한 비용이 발생하므로 수질을 적절히 모니터링하여 마모로 인한 손상을 방지하는 것이 중요합니다. 설비에는 다음으로 인한 위험이 있습니다.
- 생물 또는 광물성 물질로 인한 관 오염으로 설비의 효율성이 저하될 위험,
- 설비 부품의 부식으로 인해 설비 수명이 단축되거나 사람이 위험에 처할 위험,
- 응축수 모니터링이 불충분하여 보일러 블로우다운 공정이 더 많이 필요하여 물, 화학 물질 및 에너지 소비량이 경제적이지 않게 될 위험이 있습니다.
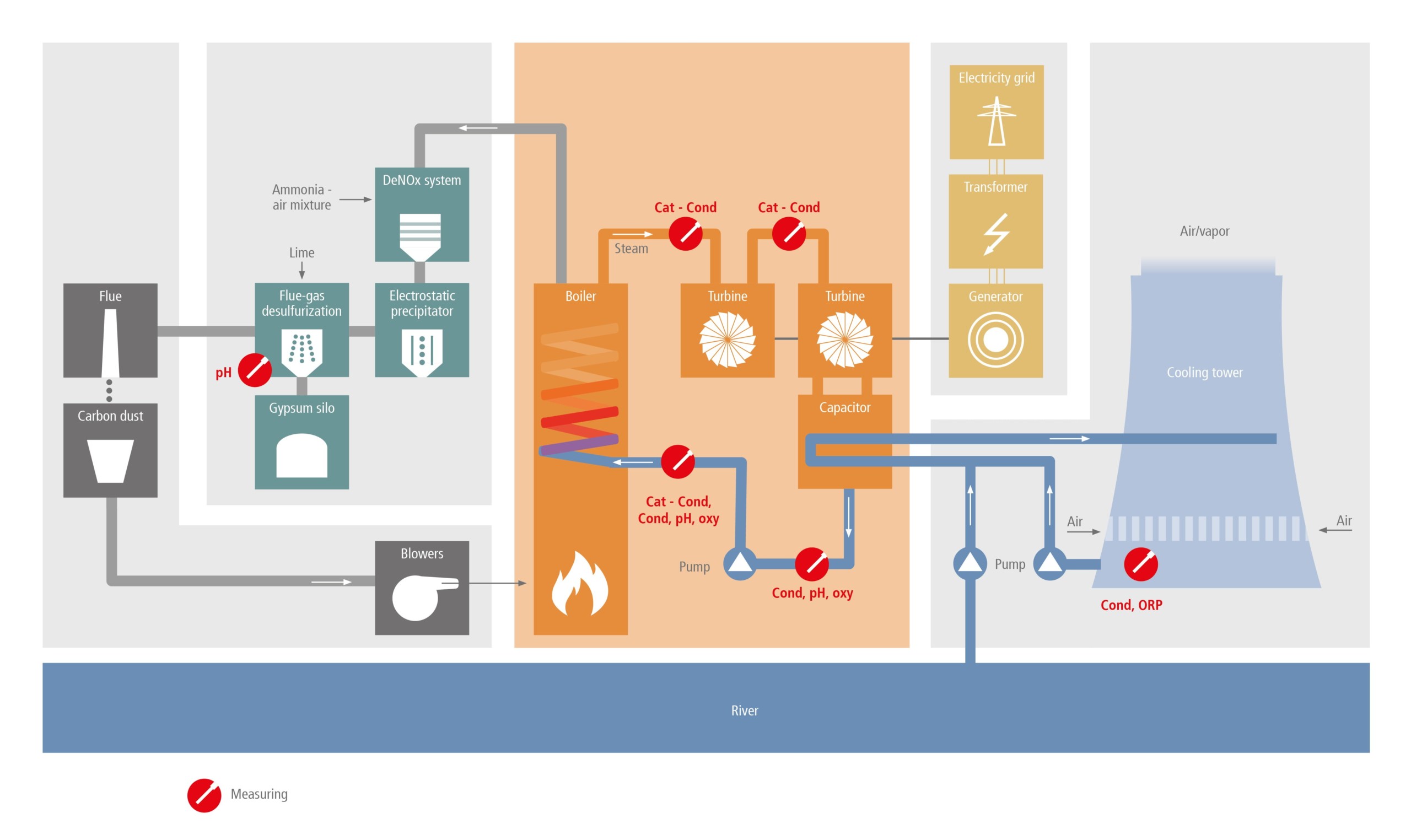
물 품질의 모니터링은 증기 발생기의 성능을 보장합니다
증기 발생기에서는 가열관에 특별한 주의가 요구됩니다. 일반적으로 증기 발생기에는 염기성 물이 공급되며, 이 물은 가열관 표면에 부식을 방지하는 얇은 산화물 층을 형성하는 장점이 있습니다. 이를 위한 알칼리화를 위해 물에 인산나트륨 및 수산화나트륨 등이 첨가됩니다. 이러한 물질을 지나치게 많이 첨가할 경우 문제가 될 수 있으므로 이러한 물질의 공급은 pH 측정의 정확한 모니터링을 기반으로 이루어져야 합니다.
크닉은 이온 활동도가 매우 낮은 액체에서도 pH 측정을 높은 정확도로 수행할 수 있도록 센서SE558을 개발했으며, 이 센서는 일반적으로 발전에 사용되는 수처리와 같은 초순수 사용 분야에서 사용됩니다.
산소는 그 부식성이 강한 특징으로 인해(농도가 매우 낮은 ppm 범위에서도 금속 표면을 부식시킵니다) 증기 발생기의 수명에 큰 영향을 미칩니다. 따라서 산소 라디칼의 결합을 위해 하이드라진과 같은 화학 물질이 사용됩니다.
센서SE707은 1 ppb의 미량 감지 한계 범위까지에서도 용존 산소를 측정하여 적절한 용량의 하이드라진을 공급할 수 있도록 합니다. 결함이 있는 가열관 또는 화학 물질의 과도한 공급은 물의 유해성분 농도를 높일 수 있으며 이러한 유해성분 농도는 일반 전도도 측정을 통해 감지할 수 있습니다.
전도도의 증가는 물의 오염도 증가를 의미하며, 이 경우 보일러 블로우다운 또는 경우에 따라 설비 검사를 수행해야 합니다. 순수, 냉각수 및 보일러 공급수와 수증기 회로에서 저전도도 및 초저전도도를 정밀하고 신뢰할 수 있도록 측정하기 위해 견고한 스테인리스강 전극이 동축으로 배치된 MemosensSE604가 개발되었습니다. 모든 Memosens 센서와 마찬가지로 SE604에는 정확한 온도 보정을 위해 온도 감지기가 내장되어 있습니다.
기존 아날로그 센서의 연결은 방수가 되지 않으므로 아날로그 제품의 제조사는 센서 내 케이블을 밀폐하여 주조합니다. 따라서 사용자는 센서 교체 시 케이블을 트랜스미터에서 분리해야 합니다. 비접촉식으로 습기의 영향을 전혀 받지 않고 측정값을 전송하는 Memosens 센서에서는 이러한 수고가 필요하지 않습니다. Memosens 센서 연결부의 유도식 측정값 전송으로 인해 습기와 외피 형성이 전송 기능을 저하하지 않습니다.
또한 디지털 Memosens 기술을 사용하면 실험실의 이상적인 조건에서 센서를 사전 교정하고 숙련되지 않은 인력이 현장에서 센서를 교체할 수 있습니다. 셀 상수는 자동으로 트랜스미터로 전송되며 추가 교정 절차에 사용할 수 있습니다.
투자
- 수익
- Memosens 센서는 재교정 또는 교체가 거의 필요하지 않기 때문에 측정 포인트 유지·보수와 새로운 센서 조달을 위한 비용이 크게 절감됩니다.
- 동시에 습도가 높은 환경에서 사용할 경우 센서의 취급이 훨씬 간단하여 특히 많은 이점을 누릴 수 있습니다. 데이터 및 공급 전압의 유도식 전송과 같은 Memosens 센서의 특징과 트랜스미터의 높은 보호 등급으로 인해 습하거나 부식성을 띄는 접촉점 또는 전자 장치에 대한 손상 등을 더 이상 고려하지 않아도 됩니다. 크닉은 트랜스미터에 대해 3년간 보증을 제공합니다.