ANALYSE DES PROCESSUS
Surveillance des process de CIP/SIP
Dans les installations pharmaceutiques, biologiques ou relatives aux process de production alimentaire, il faut régulièrement nettoyer et stériliser toutes les pièces de l’installation en contact avec le fluide. C’est pourquoi toutes les canalisations et cuves sont rincées et désinfectées avec les nettoyants alcalins et acides respectivement adaptés au process lors des procédures de nettoyage et de stérilisation appelées « cleaning in place » (CIP) et « sterilization in place » (SIP).
Lors de la SIP, l’installation de process est en plus stérilisée à la vapeur surchauffée pour procéder à une désinfection complète.
Les sondes de conductivité utilisées pour surveiller le process de nettoyage ainsi que les concentrations de produits nettoyants dans l’eau de rinçage doivent résister à des changements de température fréquents et extrêmes ainsi qu’à des nettoyants agressifs.
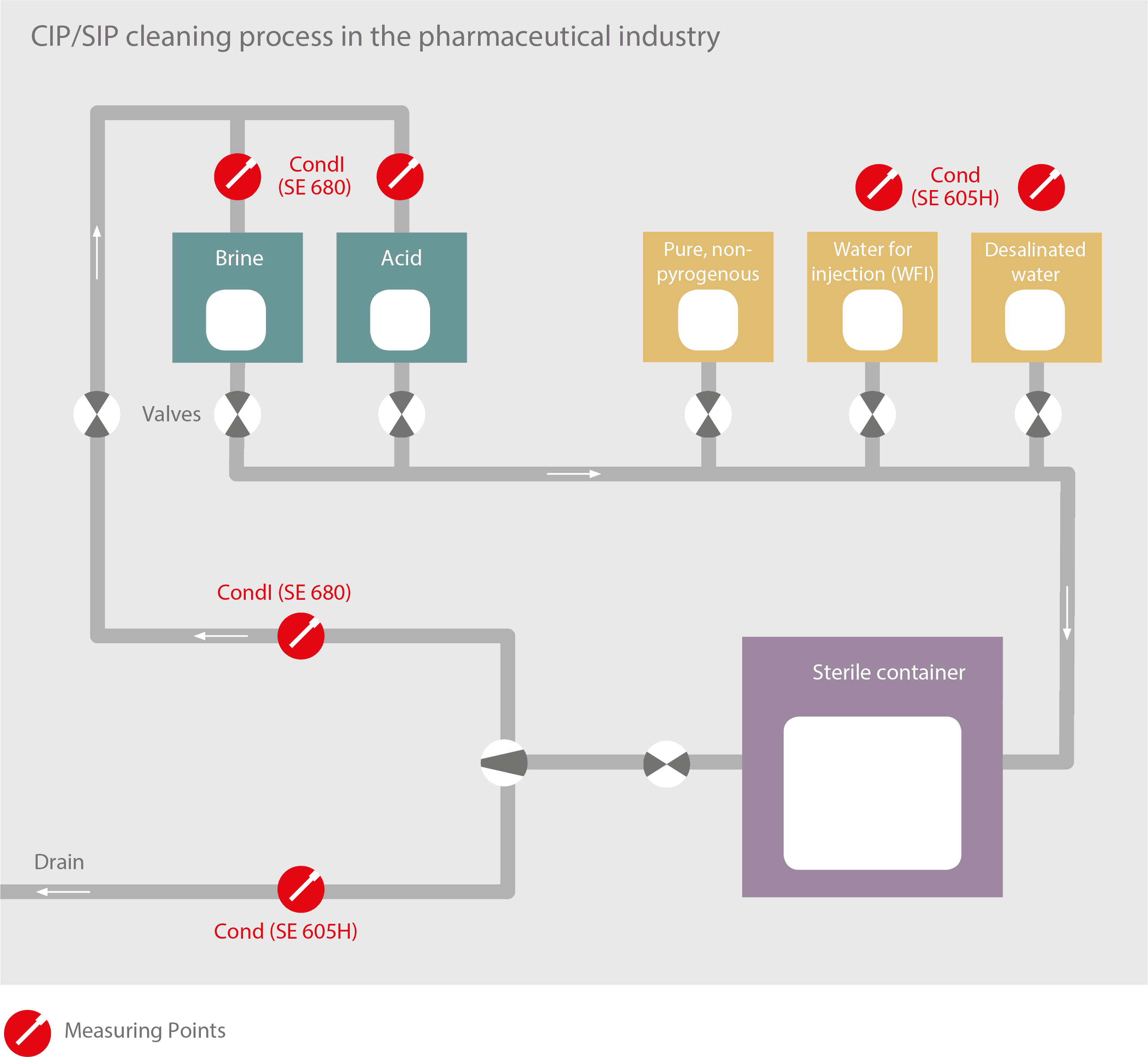
Mesure fiable de la conductivité en cas de différences de température extrêmes
Lors du CIP, les grosses impuretés sont tout d’abord éliminées par un rinçage préalable avec de l’eau et des produits nettoyants avant que les résidus de produits nettoyants ne soient évacués lors d’un rinçage ultérieur. Des liquides de nettoyage acides sont ensuite utilisés pour enlever le calcaire et d’autres dépôts minéraux, avant de procéder à l’injection de produits désinfectants et enfin au « final rinse », à savoir le rinçage final à l’eau ultra-pure.
Lors de cette procédure de nettoyage, il faut mesurer la conductivité de l’eau de rinçage après chaque étape afin d’obtenir des informations sur les substances étrangères encore présentes dans l’eau. Si les valeurs mesurées ne respectent pas les prescriptions exigées, alors la procédure en question est répétée jusqu’à ce que la valeur consigne soit atteinte.
Le process SIP peut alors commencer. Il ne consiste pas seulement à désinfecter l’installation du process, mais aussi à la stériliser en injectant de la vapeur d’eau ultrapure surchauffée(à >120 °C). Selon les process spécifiques, les tailles de lot et la variété de produits, certaines installations doivent être nettoyées et stérilisées plusieurs fois par jour, voire toutes les heures dans certains cas.
Les sondes de conductivité utilisées sont exposées à un environnement humide avec des variations de température extrêmes, qui peuvent dépasser 120 °C durant la SIP. Le design des sondes de conductivité doit être solide et surtout hygiénique. Elles sont ainsi dotées de points de raccordement au process spécifiques au secteur et sont disponibles dans des matériaux conformes aux normes de la FDA.
La sonde hygiénique de conductivité par induction SE680 destinée à la surveillance des circuits de rinçage par CIP est caractérisée par une très large plage de mesure de 0 … 2000 mS/cm pour une résolution de 2 μS/cm. Cette sonde surveille sans cesse l’ensemble du process de nettoyage.
Grâce à sa construction sans fente ni joint et à sa surface antisalissures en Virgin PEEK homologué par la FDA, la sonde SE680 résiste à de nombreuses contraintes, notamment dans l’industrie pharmaceutique.
Lors du final rinse avec WFI (water for injection ou eau pour injection), l’eau ultra-pure doit en général présenter une conductivité sans compensation de température < 2,7 μS/cm. Des valeurs plus élevées indiquent qu’il reste des résidus dans l’eau et qu’il faut donc procéder à un rinçage supplémentaire.
Pour surveiller le final rinse, on utilise la sonde conductive SE605 H, qui a été conçue pour une plage de mesure de l’eau ultra-pure de 0,001…600 μS/cm. La SE605 H bénéficie d’une construction hygiénique avec deux électrodes à géométrie coaxiale en acier inox 1.4435 électropoli avec une profondeur de rugosité <0,4 μm ou <0,8 μm. Tous les matériaux utilisés ici sont conformes aux normes de la FDA.
Pour la transmission des valeurs mesurées des sondes Memosens au système de commande, vous pouvez choisir les transmetteurs industriels MemoRail, qui transfèrent directement les valeurs et les températures des sondes au système de commande par le signal de sortie de 4-20 mA. Pour les systèmes de commande basés sur Modbus, il existe aussi une variante MemoRail avec l’interface correspondante. En tant qu’appareil multiparamètres dans un boîtier pour montage en série compact et peu encombrant, MemoRail est une solution universelle à un ou deux canaux pour toutes les sondes Memosens de mesure du pH/redox, de l’oxygène et de la conductivité.
Retour sur investissement
- La technologie Memosens met l’accent sur la rentabilité du poste de mesure. L’utilisation de Memosens permet de réduire considérablement les coûts d’investissement associés à la technique de mesure analytique. La version à 2 canaux du transmetteur industriel multiparamètres MemoRail permet de raccorder deux sondes Memosens simultanément. Le boîtier pour montage en série élancé et compact simplifie son installation dans n’importe quelle unité, même en cas d’espace réduit, et transmet directement les signaux de mesure au système de commande par 4-20 mA ou Modbus.
- La technologie Memosens réduit et simplifie la maintenance du poste de mesure puisque les données de calibrage sont directement enregistrées dans la tête des sondes Memosens. Les sondes de conductivité numériques solides surveillent ainsi le process de façon fiable et précise.